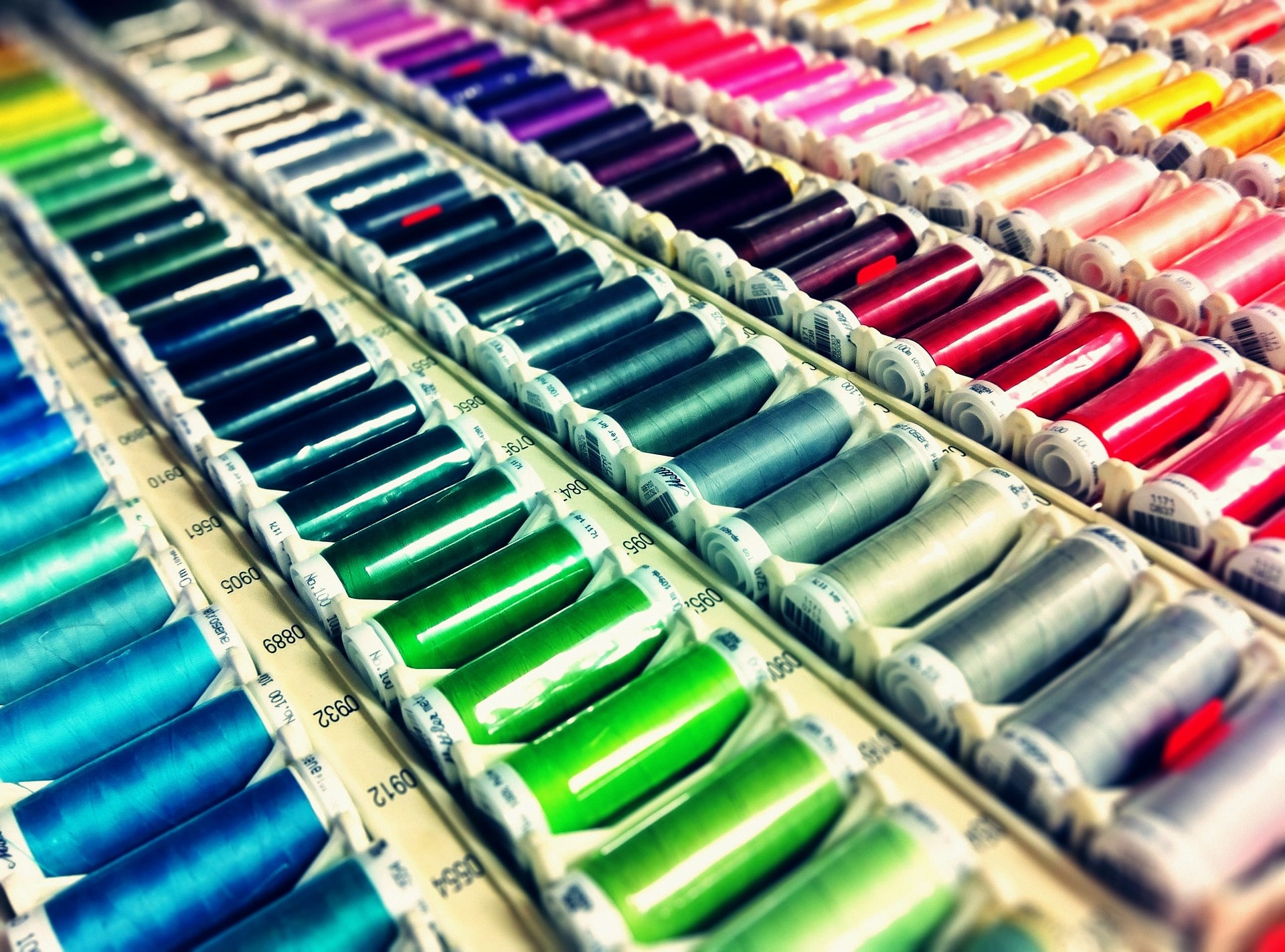
Materials management (MM) refers to the business processes involved in managing the flow of materials from the supplier to the manufacturer, followed by the manufacturer maintaining sufficient inventory at its end to ensure a smoother supply chain. As a leading ERP company, SAP provides multiple solutions for companies looking to perform MM.
Table of Contents
As part of the supply chain, SAP MM is a key driver in the logistics landscape of a business. Without it, the entire supply chain falls apart. It helps meet market demand by performing activities such as planning stock levels, minimizing work-in-process inventory, fulfilling customer orders, and collaborating with suppliers and other vendor partners.
MM revolves around three flows:
A material flow is focused on the materials themselves, and how they move from supplier to customer. Material flows begin when raw materials are ordered from a supplier, continue as the materials are turned into finished products, and typically end when headed out into transportation channels. In cases where returns are made by customers, the material flow process will continue as the product is sent back to the manufacturer.
An information flow is focused on order management, things such as delivery status and order turnaround time. This is important for providing transparency between the business and its customers, many of whom are looking for accurate and real-time information about the status of their orders.
A financial flow is focused on the value of the materials being used in the creation of a product. This is important for calculating values such as cost of goods sold (COGS) and for maintaining accurate bookkeeping in areas such as inventory accounts and accounts payable.
In addition to these flows, SAP MM plays an important role in larger and end-to-end business processes, such as:
In the procure-to-pay (sometimes called source-to-pay) process, users identify the raw materials they need to produce certain products, solicit quotes from suppliers, and choose the best offer for their manufacturing needs. Since this deals with acquiring materials, the material and financial flows are affected.
In the plan-to-product (sometimes called design-to-operate) process, businesses select the amount of raw and packing materials they need from their inventory and begin work on creating the product. Since this deals with movement of materials within the production warehouse, the material and financial flows are affected, including the actual costs incurred to produce the product.
In the order-to-cash (sometimes called lead-to-cash) process, businesses collect and fulfill orders from customers via sales orders. Since this deals with the movement of products and orders, the material, information, and financial flows are affected.
When companies maintain their plants with SAP Plant Maintenance or SAP S/4HANA Asset Management, spare parts and other consumables have to be procured and stored before they can be used (when necessary) and to ensure effective maintenance management. This inventory management falls under the purview of SAP MM.
Similar to maintenance management, as businesses look to expand or rebuild their plants and production equipment by purchasing assets, equipment, machinery and materials for the projects, the associated inventory of parts that go into such a capital project fall under the SAP MM umbrella.
SAP currently maintains two expansive ERPs (oftentimes referred to as “business suites”) for its customers. Both SAP ERP and SAP S/4HANA provide users the ability to perform MM tasks.
SAP ERP is SAP’s legacy business suite, and includes a massive SAP Materials Management component that houses MM data. SAP ERP will be maintained by SAP through 2027 with some additional, extended maintenance planned through 2030.
SAP S/4HANA is SAP’s current enterprise application suite. First released in 2015, it drastically simplifies processes compared to SAP ERP, and consists of numerous lines of business (LoBs) which also cover a host of business processes. The SAP S/4HANA Supply Chain, SAP S/4HANA Sourcing and Procurement, and SAP S/4HANA Manufacturing LoBs pertain to SAP MM.
SAP is continually expanding its product functionality across all products, and the MM area is no exception. One of the most important MM-related features that SAP has introduced is the Material Ledger, a way to record, valuate, analyze, and report on inventory. With SAP S/4HANA, implementation of the Material Ledger becomes mandatory.
Another change to MM in SAP S/4HANA is the reorganization of the “customer” and “vendor” terminology found in SAP ERP. In the new suite, both fall under the term “business partner.”
As SAP continues to explore different intelligent technologies such as AI and robotic process automation, further SAP MM enhancements are expected to be delivered to customers.
Materials management functionality is only one part of logistics, and it fits in alongside other SAP ERP modules and SAP S/4HANA LoBs to fulfill its main goal of getting products from conception to customer. Here’s an overview of key integrations:
It’s important to know how much of a product to create in order to meet demand, but also not have large amounts of unsold inventory sitting around. With production planning operations, businesses use historical data and other market demand signals to create a sales forecast and determine how much product to make in order to meet that forecast.
Once production begins, it’s important that the finished product meet certain standards imposed by the manufacturer, the customer, and in some cases, regulatory agencies. Quality management operations helps define those standards and aid businesses in selecting raw materials vendors, inspecting prototypes and products in production, and ensuring the final product is of a high quality.
Once a product is created, inventory levels and locations need to be managed. With warehouse management operations, businesses manage day-to-day warehousing operations, focused largely on stock. This includes picking and packing items when orders come in, and moving goods into, out of, and around the warehouse.
Goods will eventually need to be moved between point A and point B (or point C, D, etc.). Transportation management operations relate to these movements: how they occur, when they occur, and how to account for stock in transit, among others.
Organizations also take care of their fixed assets—the tools needed to create products, and the warehouse and vehicles used to move it around and to customers. With plant maintenance (or “enterprise asset management”) operations, businesses manage the wear and tear of these assets through preventive maintenance to ensure they are always ready for use as needed.
Once a product has been created and is awaiting dispatch, orders need to be formally acquired from customers before it can be shipped out. Sales and distribution operations focus on generating orders and getting the product out the door and to its final destination.
Finally, payment must be procured when a product is sold to a customer. FICO operations, while not a logistics topic per se, is tangentially related to MM as this is the area of the business that requests, records, and remedies payment-related aspects of the procure-to-pay, order-to-cash, and plan-to-product processes. Accounting for COGS and other production-related expenses are also accomplished in the FI and CO modules in SAP ERP and in SAP S/4HANA Finance.
While we’ve laid out much of the important terminology you’ll run into when performing materials management, there are a handful more concepts that will be helpful to you.
Learn more SAP from our official Learning Center.
And to continue learning even more about SAP MM, sign up for our weekly blog recap here:
On our website, we use cookies that enable certain website functionalities (such as the shopping cart), and cookies that help us improve your user experience and our service offerings. By clicking Agree and Continue, you confirm that you are at least 16 years old and that you give Rheinwerk Publishing and its third-party providers consent to set these cookies, and to process the respective personal information regarding your website visit. You can also make individual choices and select which cookies you allow. By clicking Decline, you decline all cookies that are not necessary for the full website functionality. You can withdraw, review, and change your consent at any time by clicking on the link „Change Privacy Options“ in the website footer. You can find more information in our privacy policy.
Name | Technology | Collected Data | Retention Period | Purpose |
---|---|---|---|---|
csrftoken | Cookie | UUID | 364 days | Security token for transmitting forms |
inc_sessionid | Cookie | UUID | 28 days | Cookie for log in and shopping carts |
bo_sessionid | Cookie | UUID | Session | Cookie for log in |
oscar_open_basket | Cookie | Integer (Basket-ID) + Hash | 7 days | Cookie for shopping carts |
list_style | Cookie | String | Session | Storage of layouts selected |
bg_consent | Cookie | true/false | 180 days | Consent Microsoft Advertising ("Bing") |
ga_consent | Cookie | true/false | 180 days | Consent Google Analytics |
gt_consent | Cookie | true/false | 180 days | Consent Google Ads Tags |
hj_consent | Cookie | true/false | 180 days | Consent Hotjar |
hs_consent | Cookie | true/false | 180 days | Consent HubSpot |
sa_consent | Cookie | true/false | 180 days | Consent Impact |
ws_consent | Cookie | true/false | 180 days | Consent necessary website functionality |
yt_consent | Cookie | true/false | 180 days | Consent YouTube |
Cookie Name | Retention Period |
---|---|
brwsr | 720 days |
IR_PI | 720 days |
IRLD | 180 days |
IR_GBD | Expires when the session ends |
IR_{Campaign_ID} | Expires when the session ends |
EPERSIST | Expires when the session ends |